Test in Lab
The following information presents an objective study carried out in an independent laboratory. It’s based on a representative number of electromagnets, at first sight all equivalent, sold on the European door locking market..
Pictures of brand new electromagnets before going through the corrosion resistance test:
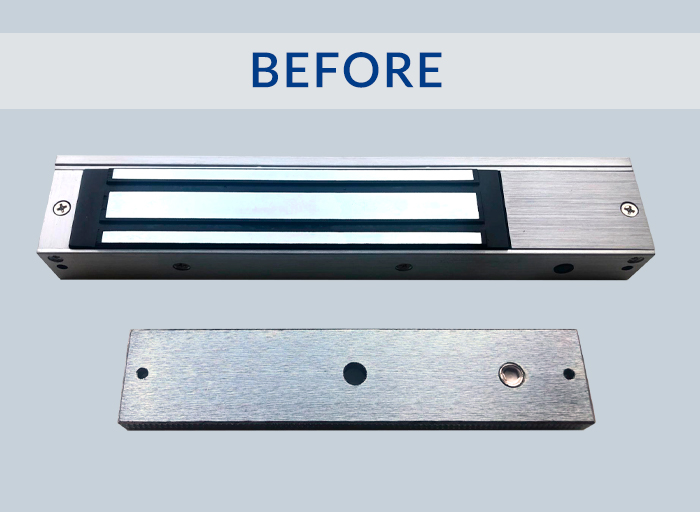
Pictures of the same electromagnets after the 96h corrosion test, ISO 9227/ASTM B 117:
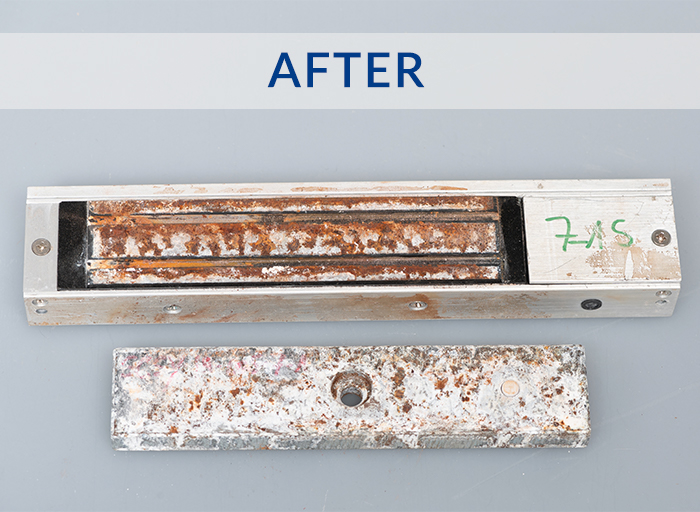
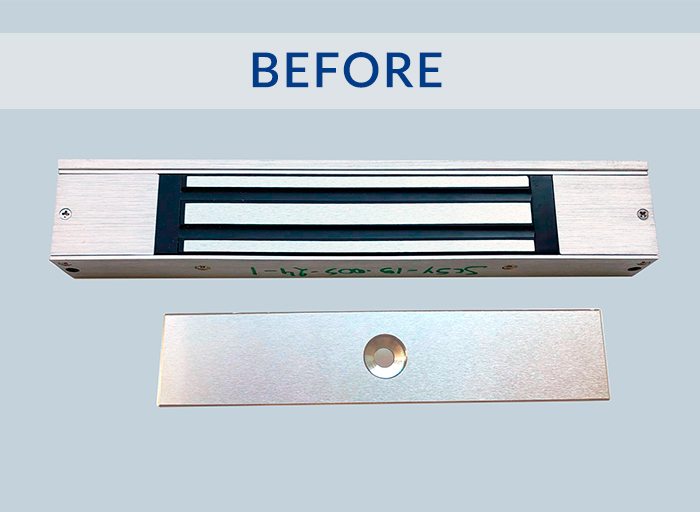
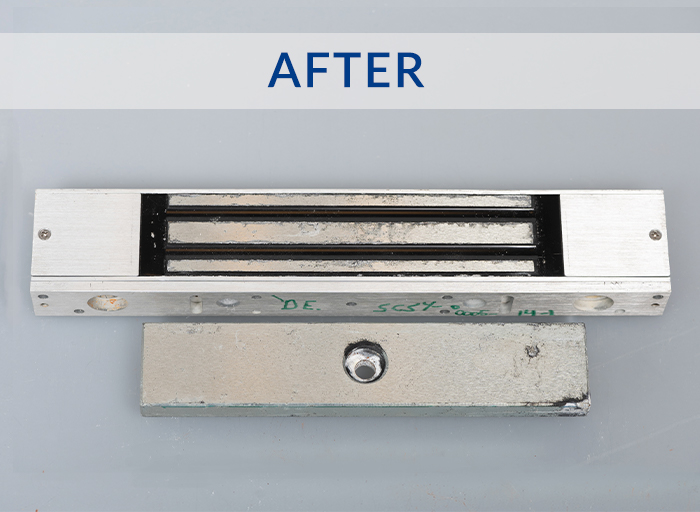
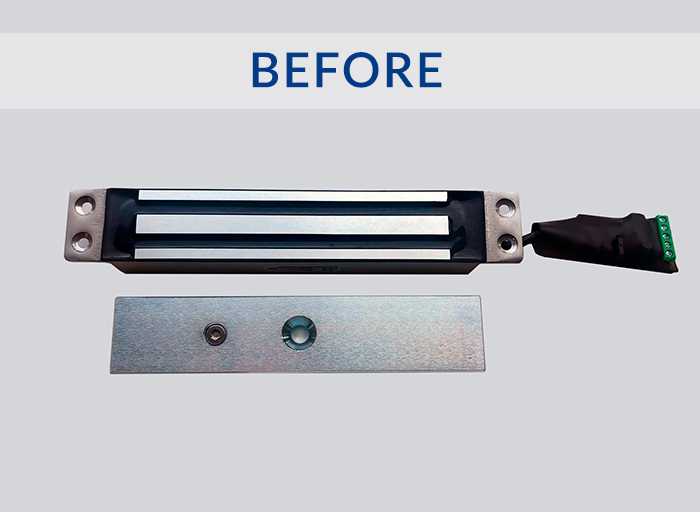
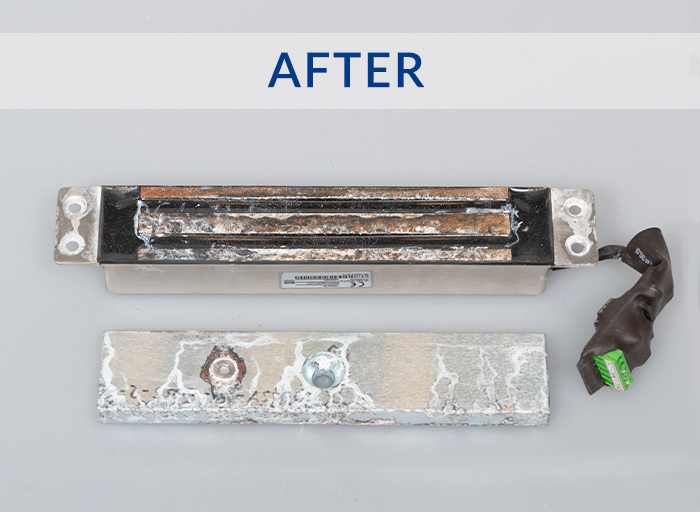
Summary table of the laboratory tests performed
European Laboratories CSTC – Centre Scientifique et Technique de la Construction (Scientific and Technical Construction Centre)
1- Figures and diagram on the surface electromagnets holding force:
Announced, tested and corroded
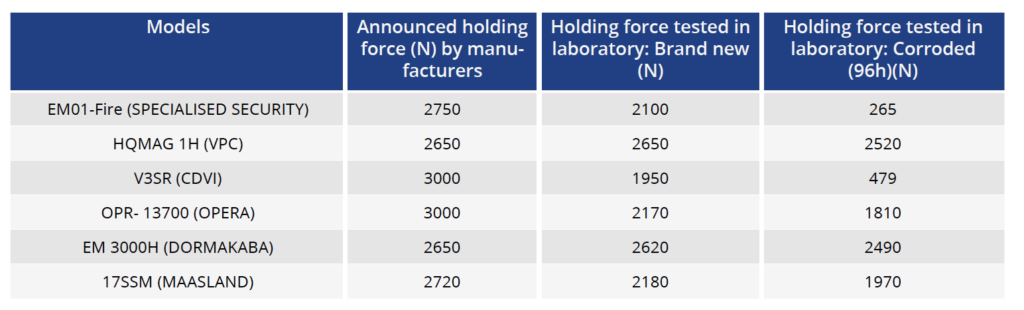
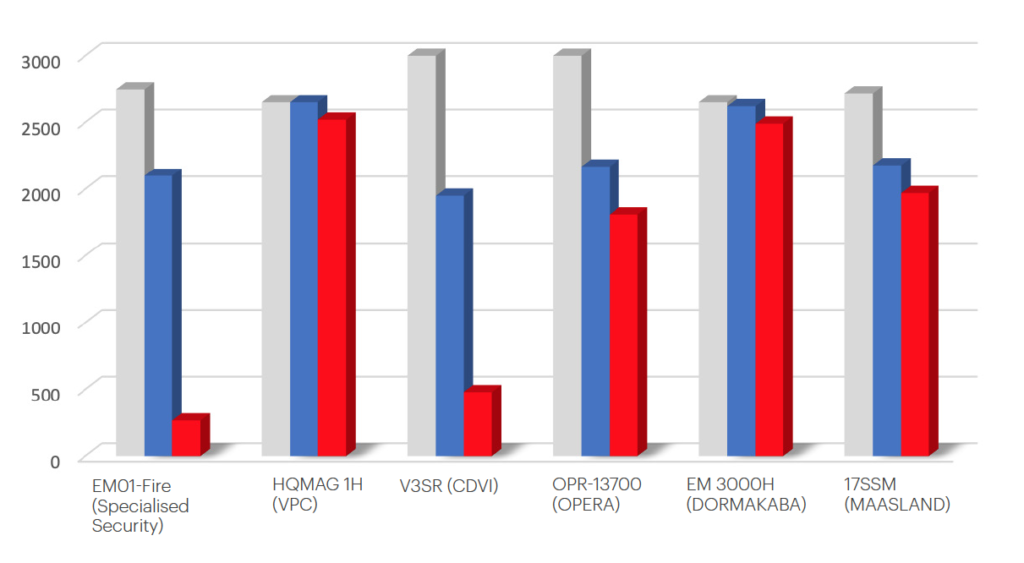

2- Figures and diagram on the mortise electromagnets holding force:
Announced, tested and corroded
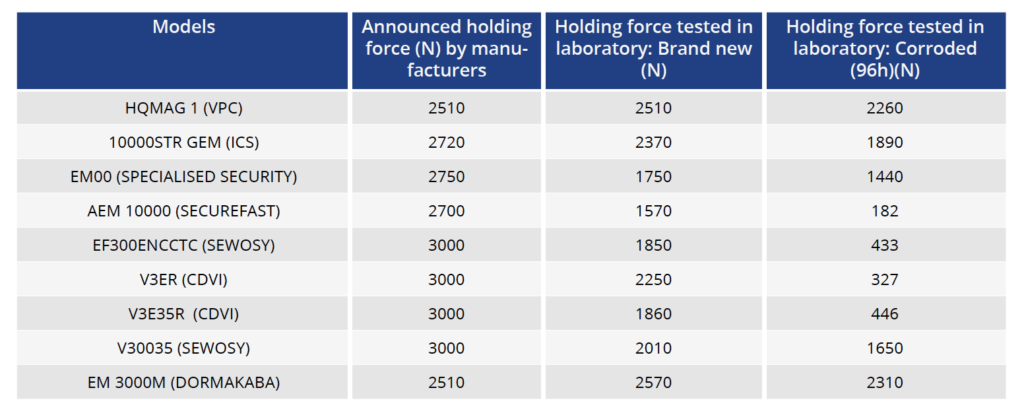
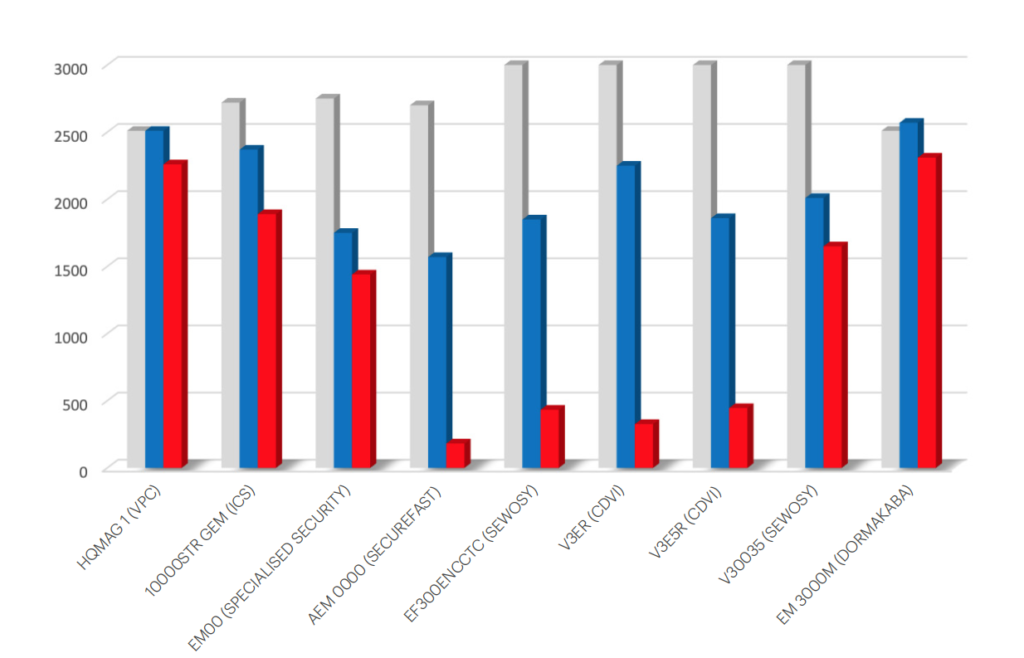

*Tests made at CSTC Laboratory (Centre Scientifique et Technique de la Construction) – BBRI (Belgian Building Research Institute) in October 2020
Power supply: 12 VDC
Traction speed: ~3mm/sec
White paper: Electromagnets in Europe
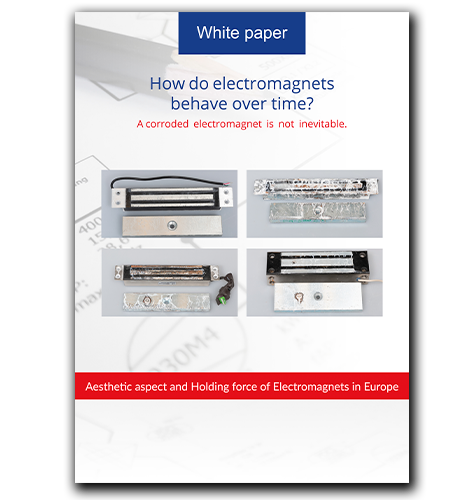
A white paper is a communication tool intended to be used as a practical guide for readers. It addresses a predefined problem and helps readers to choose a solution or take a decision.
The electromagnets market is experiencing criticism as to the real security provided by this locking mode. This white paper aims to shed light on this problem by analyzing a large sample of electromagnets.
To attest to the level of quality, and therefore of safety, guaranteed by these samples, this study notes, product by product, the initial holding force but also the resistance to corrosion and its impact on the final holding force of this panel of electromagnets.
Methodology
1. Purchasing Phase
The electromagnets tested came from several official distributors located in Europe. The “300Kgf” models that were chosen are the most commonly sold ones on the European market. The tested products did not undergo any manipulation or modification. No intentional external factor was likely to influence the test results.
2. Three step testing phase
The tests were performed in 3 separate stages, on two identical electromagnets from each manufacturer and/or distributor.
- Holding force test on brand new electromagnets: A first brand NEW electromagnet is tested on an axial testing machine in order to find out its maximum strength.
- Corrosion-proof test: The same electromagnet is subjected to a salt spray test in the same laboratory according to the standards ASTM B 117 / ISO 9227.
- Holding force test on the same maglock after the salt spray test: The electromagnet emerging from the salt spray test, representing outdoor usage for an appreciable length of time, is tested in the same axial testing machine to obtain the residual holding value of a electromagnet oxidised as a result of time or its environment.
3. Editorial phase
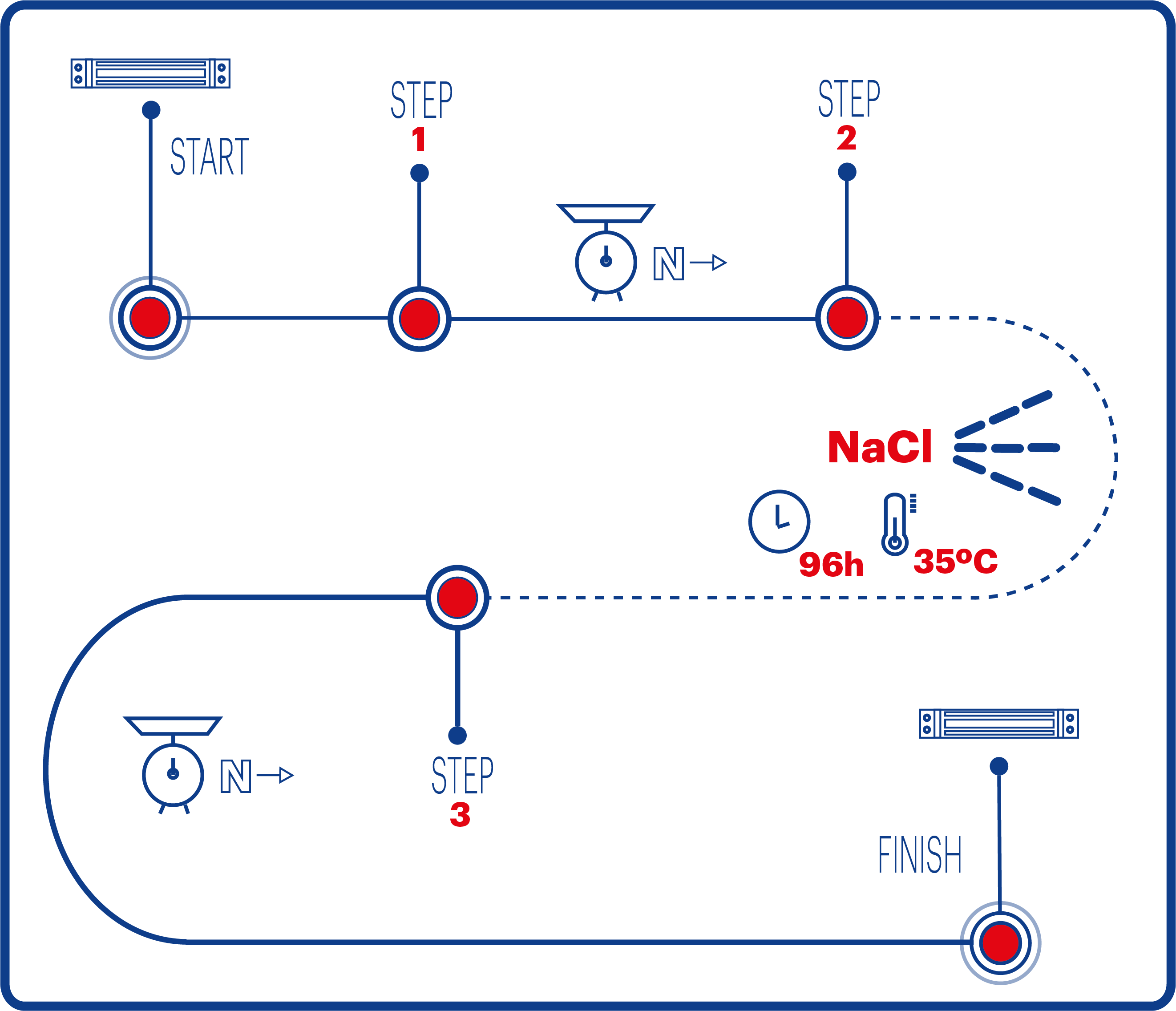
The last phase was also performed in 3 stages.
- Independent laboratory reports: The laboratory issued the various reports related to each product tested according to the procedure described above.
- White paper drafting: This objective and educational document exists to allow readers to understand the ins and outs of tests performed in the laboratory in terms of safety and security.
- Verification of legal compliance: The procedures followed throughout the tests and all of the information disclosed in relation to the tests were verified and validated by a specialist law firm. Once again, the objective for this approach was to verify that the quality level available on the electromagnet market reflects the truth, the whole truth, and nothing but the truth!
Physical phenomenons: Having an impact on the locking performance of an electromagnet
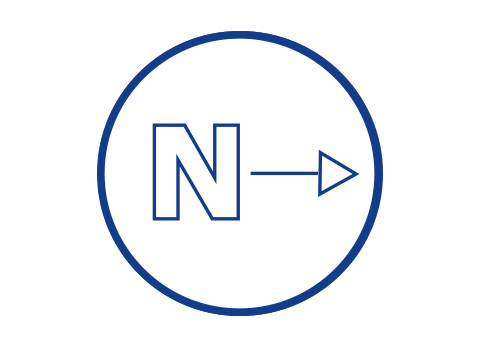
1. Holding force
This is what provides locking on installation and also over time, as long as the installation is performed according to the best practices of the trade.
This mainly depends on the quality of the materials used. Unfortunately, at this time (Summer 2020), there are no standards or official texts in Europe, although standardised tests are commonly used in the factory and by many laboratories using an axial force machine.

2. Corrosion resistance:
This is a crucial matter that is nevertheless deliberately swept under the carpet by some.
A electromagnet that has been poorly treated or not treated at all will initially have a pulling force that is somewhat superior to its normal but which will quickly but slightly diminish when rust oxidation attacks the flat surfaces.
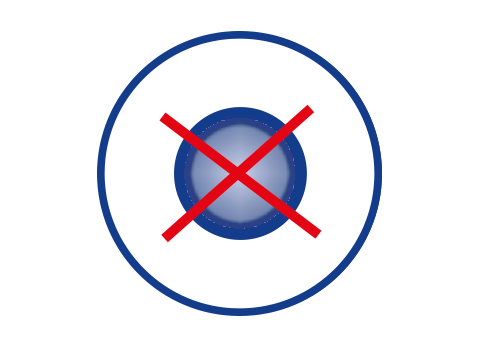
3. Residual magnetism or “magnetic remanance”:
This is an insidious defect as it only appears after a certain amount of time.
How to get arount it?
« Mechanical repeller »
Most of the maglocks available on the market attempt to compensate for this defect by adding a small disc mounted on the backplate and known as a “repeller”. As well as upsetting the balance of the magnetic field and therefore the holding force of the lock, this mechanical trick is very unreliable and renders the lock dangerous when it becomes ineffective and can no longer compensate for the endemic defect in this type of lock.
« Le Kick-off »
It involves an invisible electronic repeller which is meant to compensate a residual magnetic force, of a necessarily random value, by the hysteresis effect of an inverse current, the value of which is arbitrarily determined. Since the wear or breakdown (MTBF) of a kick-off system is invisible, unlike a mechanical repeller, the electromagnet can suddenly become a permanent magnet with serious consequences for people’s safety.
“The intrinsic absence of remanence”
Only electromagnets designed to inherently show no magnetic remanence require no mechanical or electronic repeller (kick-off) to compensate the residual magnetism. They immediately release access, as soon as the power supply stops, without any time limit. (MTBF = ¥).
Conclusion:
What is expected of a electromagnet?
- To have sufficient retaining force, at least equal to the amount claimed, + ou – 10%
- To have received very effective corrosion treatment
- To have no magnetic remanence even 30 years after continuous use.
Materials: the quality of the raw materials is essential for the proper functioning of the end product.
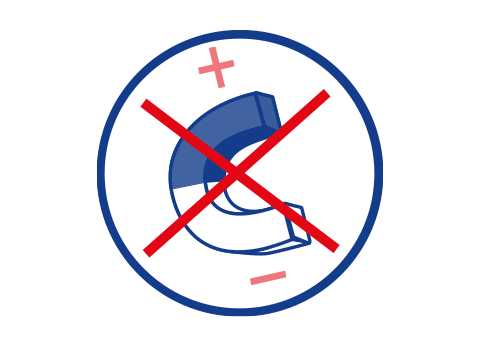
a: The steel Grade
Finding the right balance between anti-corrosion treatment and holding force.
The types of steel and alloys are practically infinitely variable in number and quality. The challenge presented in designing an electromagnet is finding the right balance between magnetic permeability and corrosion resistance. However, the more stainless a steel is, the less magnetic it is!
Finding the alloy that will INTRINSICALLY lack residual magnetism.
The steel is also a “magnetisable” metal. It is sufficient to place a steel tool, such as a screwdriver, on a permanent magnet, to see that it also becomes a magnet.In the design of an electromagnetic locking it is essential for the safety of the users, to prevent the steel of the maglock or its armature plate from becoming a permanent magnet. Only special and qualitatively superior steels meet this essential criterion.
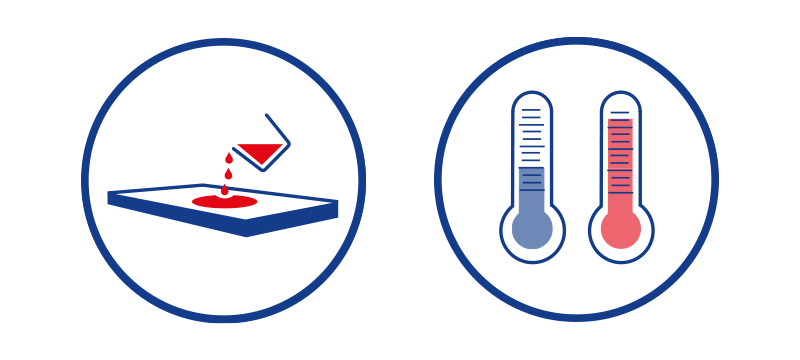
b: Resin quality:
This makes a wide range of temperature variations possible (-60°C to 80°C)
The electromagnet’s resin must be particularly resistant to the wide temperature ranges encountered in the field. In certain conditions, under the sun in the deep south, for example, the temperature of an electromagnet can exceed 80°C. In northern Europe, or in cold rooms, it can go as low as -60°C. Despite these extreme conditions, the resin used cannot crack or melt. Failing that, the consequence would imply permanently “gluing” the electromagnet to its armature plate.
Design tip when pouring resin
The resin’s height between the magnetic strips is precisely calculated so that the difference in values between its thermal expansion and that of the steel never affects the quality of the electromagnet regardless of the conditions of use.
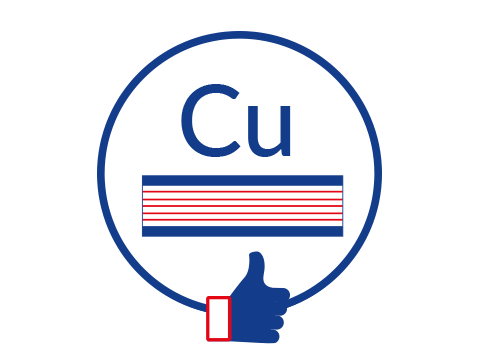
c: Copper grade
Obtaining the best possible performance: Energy consumed vs. Holding force generated
The magnetic field of an electromagnet is generated by one or more copper windings. It is transmitted and amplified by the structure of the steel. The performance depends on the copper grade: Electricity consumed in relation to the armature plate’s holding force.
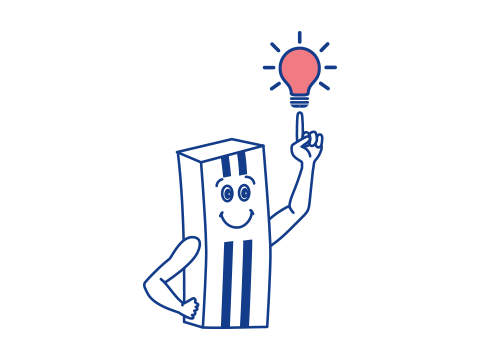
What every locksmith professional should know:
Basic values:
• Since the magnetic is of US origin, its force was originally expressed in pounds (lbf)
• One lbf is equivalent to 0.453 kgf. A 1,200 lbf lock therefore has a holding force of about 540 kgf.
• One kilogram-force (kgf) is not a kilogram of weight (kg). It is therefore more correct to use the unit of measure for force, that is, the Newton.
• 1 kgf = 9.80N = 2.20 lbf